Why EMI Keeps Ruining Your PCB Designs (And What to Do Before It’s Too Late)
- Dario Fresu
- 2 days ago
- 7 min read
Electromagnetic interference (EMI) remains a major challenge in printed circuit board (PCB) design, frequently transforming a promising layout into a source of frustration. With the increasing complexity of electronic systems—characterized by high-speed data rates, densely packed components, and tighter compliance standards—EMI in PCB design cannot be ignored. The consequences are significant: radiated emissions can lead to failed certifications, costly redesigns, or unreliable products. The crucial understanding is that most PCB EMI issues arise internally, rather than from external sources. By tackling EMI at its origin, you can prevent these problems from escalating.
The Hidden Drivers of EMI in PCB Design
EMI results from the complex interaction of electromagnetic fields (EM fields) within a PCB. These fields, produced by currents flowing through the board’s traces, components, and planes, become more problematic as modern designs strive for higher performance. High-speed signals, marked by sharp transitions and high frequencies, increase the intensity and variability of these fields. The demand for smaller, denser boards leads to compact layouts, reducing the distance between signal paths and intensifying coupling effects. Additionally, smaller form factors limit the space for implementing effective signal integrity practices. By understanding these fundamental causes, engineers can apply targeted mitigation strategies to ensure robust and compliant PCB designs. Let's explore the main causes.
Stackup Choices Set the Stage
The PCB stackup is crucial for managing EMI, going beyond just choosing the number of layers. A well-designed stackup controls electromagnetic fields by providing proper reference planes and reducing coupling, while a poorly configured one can increase radiated emissions. For example, placing a high-speed signal layer next to a power plane without an adjacent return and reference ("ground") plane as a low-impedance return path, increases parasitic capacitance and impedance mismatches, causing electromagnetic energy to radiate as noise.
Single-layer stackups, once common, are unsuitable for modern designs, where signal rise times in the nanosecond range create high-frequency harmonics that require effective field containment. Similarly, double-layer stackups with signals on both layers struggle to maintain signal integrity without a dedicated return and reference plane (RRP), as return currents are forced into larger loops, increasing EMI. Modern integrated circuits (ICs), with shrinking rise times and expanding signal bandwidths, generate harmonics that heighten EMI risks, leaving little room for error. These demands require best practices in signal integrity, such as multilayer stackups with continuous return and reference planes, to confine fields, reduce loop areas, and effectively suppress emissions.
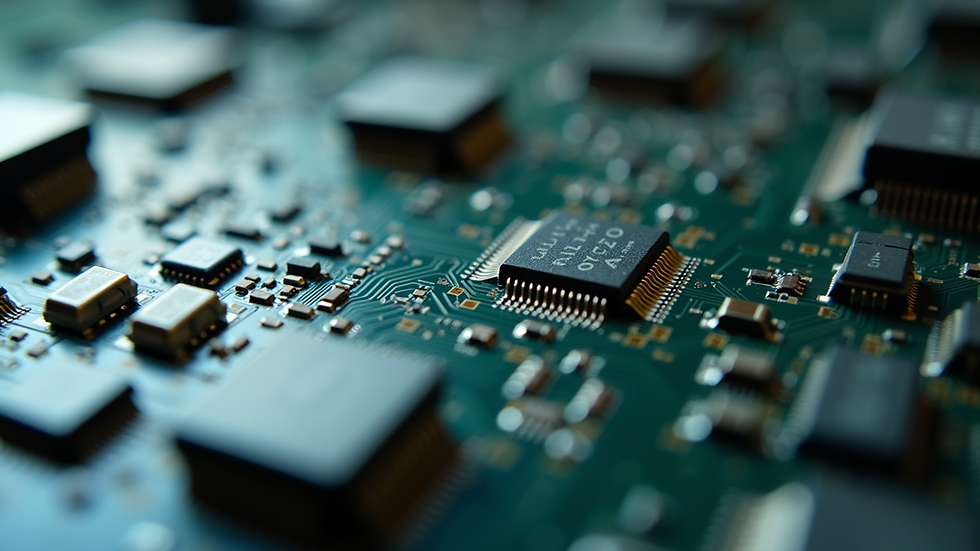
For a 6-layer PCB, with a SGN-RRP-PWR-SGN-RRP-SGN stackup, each signal layer gains a low-impedance return path from its adjacent return and reference plane. This arrangement minimizes the loop area enclosed by the signal current and its return, constraining the magnetic fields that drive radiated emissions. The relationship governing EMI is captured in a simplified form: the radiated electric field strength (E) in the far field is approximately proportional to the loop area (A), current (I), and frequency (f), expressed as E ∝ I × A × f. While this omits higher-order effects like distance and frequency-squared dependence, it illustrates a key principle: reducing A directly lowers E. By positioning signal layers close to their RRP, this stackup shrinks the loop area, curbing EMI at its source while enhancing signal integrity through reduced crosstalk and impedance variations.
Understanding Impedance Discontinuities: Causes and Effects
Impedance mismatches along signal paths significantly contribute to electromagnetic interference (EMI). When a trace experiences a sudden change in characteristic impedance, such as moving through a via stub or crossing a split ground plane, part of the signal's energy is reflected back due to the discontinuity. These reflections not only harm signal integrity by causing ringing or distortion but also radiate as EMI when they couple to traces or structures acting as antennas. For example, a 50-ohm trace encountering a 70-ohm via stub at 3 GHz, results in a reflection coefficient of 0.167, reflecting about 17% of the signal voltage. At this frequency, the reflected energy can activate resonant paths on the board, effectively turning it into an unintentional radiator and increasing EMI emissions.
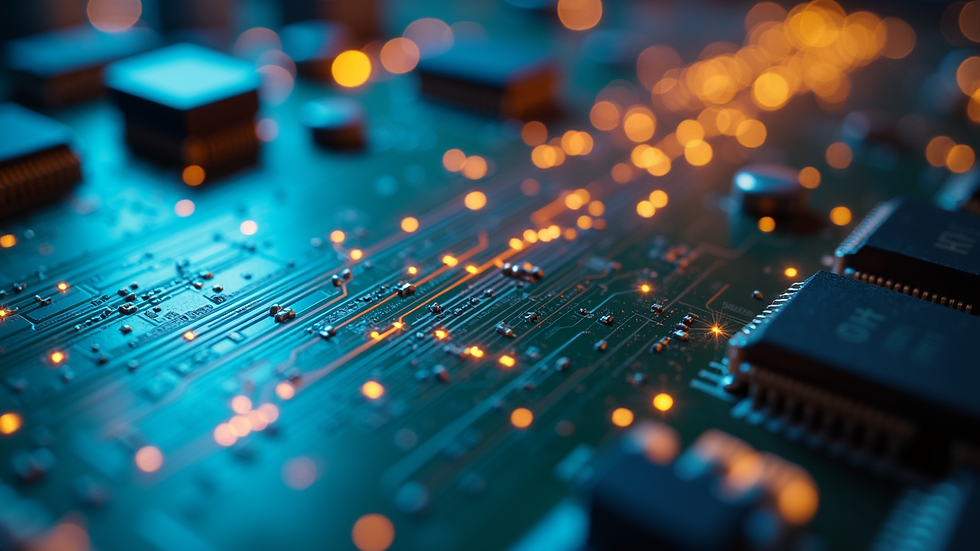
Modern electromagnetic simulation tools like SIMBEOR® enable engineers to predict impedance discontinuities by modeling signal paths, vias, and plane structures, identifying potential EMI sources before fabrication. However, effective mitigation begins with intentional design practices: ensure trace widths and via geometries maintain consistent characteristic impedance, and avoid routing signals over gaps in reference planes that disrupt return currents. The relationship is straightforward—by minimizing impedance variations, reflections are reduced, curtailing EMI at its source and preventing radiated emissions from escaping the PCB.
Signal Reference Integrity: The "Grounding" Game Changer
In contemporary PCB design, "grounding" has shifted from using a single connection to adopting low impedance return and reference techniques, particularly in high-speed scenarios. A solid, continuous return and reference plane below a signal layer offers a low-inductance return path, which minimizes current loop areas and reduces electromagnetic emissions. If this reference is interrupted, like when a high-speed trace crosses a split plane, return currents must detour around the gap, enlarging the loop area, strengthening the magnetic field, and increasing radiated emissions.
Consider a differential pair: if one trace is aligned with a continuous return and reference plane while the other crosses a plane split, this causes an impedance mismatch, generating common-mode noise, a major source of EMI, due to unequal return paths. To manage signal return and reference, it's essential to use local return and reference vias with continuous planes, ensuring consistent signal reference integrity, especially where short rise times and wavelengths demand tight control. This is not merely theoretical; ensuring uniform return paths results in measurable reductions in emissions, as evidenced by lower radiated noise levels in practical testing.
EM Fields and Layout: The Direct Link
Layout decisions critically shape the behavior of electromagnetic fields in PCB design. A long, unshielded trace behaves like a dipole antenna, radiating power that scales approximately as P ∝ (L × f)², where L is the trace length and f is the signal frequency, assuming constant current. At 5 GHz, with a wavelength of about 2.8 cm in FR4, a 10 cm trace—over three times the wavelength—emits significantly more radiated energy than a 2 cm trace, with power increasing roughly 25-fold due to length squared. This effect intensifies when routing high-speed signals near board edges or leaving them exposed, as unconfined fields couple to adjacent structures like enclosures or external cables, amplifying EMI.

The solution? Reduce trace lengths, route them inward, and position signals between ground planes. These layout adjustments directly minimize the spread of EM fields, decreasing EMI without relying on external aids.
The Cost of Letting EMI Run Wild
Overlooking these factors is more than a technical oversight—it's a business risk. Radiated emissions can push a design past FCC or CE limits, delaying certification. Redesigning to resolve PCB EMI issues can cost tens of thousands in engineering hours and delay time-to-market. Even worse, if EMI issues reach production, they can lead to field failures that undermine customer trust—imagine a medical device malfunctioning or an automotive sensor failing.
By 2025, compliance requirements are becoming stricter. New EU EMC directives require lower emissions across broader frequency bands, and automotive standards like CISPR 25 are stringent. The message is clear: address EMI in PCB design early, or face the consequences later.
Initial Steps to Minimize EMI in PCB Design
What proactive actions can you take to prevent issues before they occur? Below are practical starting points with modern, source-focused EMI design tips that establish a foundation for successful results. Although this isn't a comprehensive guide, these strategies will guide you toward achieving cleaner designs.
Early Stackup Optimization :
Initiate your PCB design with a ground-centric stackup that prioritizes continuous return and reference planes as low-impedance return paths. For high-speed applications, emphasize symmetry by alternating signal and RRP layers to tightly confine electromagnetic (EM) fields, reducing loop inductance and radiated emissions. Leverage simulation tools like SIMBEOR® to evaluate stackup performance, analyzing characteristic impedance, crosstalk, and field containment, before committing to fabrication. This early optimization locks in robust EMI control and signal integrity, averting expensive revisions later in the design cycle.
Maintain Impedance Control:
Meticulous design of signal paths is essential to minimize EMI and preserve signal integrity in high-speed PCBs. Employ controlled-impedance traces, typically 50 ohms for single-ended or 100 ohms for differential digital signals, calibrated to the stackup’s dielectric constant, trace width, and layer spacing. Techniques like back-drilling vias eliminate stubs, preventing impedance discontinuities that reflect energy at gigahertz frequencies. Similarly, avoid routing traces over plane splits, which force return currents to detour, enlarging loops and amplifying emissions. Even a 10% impedance mismatch, say, from 50 to 55 ohms, can markedly elevate radiated emissions at GHz frequencies, where short wavelengths and strong harmonics turn small reflections into significant noise sources. Consistent impedance control across all signal paths is thus non-negotiable for robust performance.
Secure Signals with Strong Return and Reference Planes:
Avoid using single-point "grounding" for high-frequency signals; instead, utilize solid, continuous return and reference planes to improve performance. Connect these planes with vias placed near signal transitions to ensure effective return paths. Testing this configuration with a near-field probe is likely to demonstrate reduced emissions as the integrity of the return and reference paths is enhanced.
Manage EM Fields Through Layout:
Keep high-speed traces short and centralized to minimize EMI. Route these traces between return and reference planes to contain EM fields, thereby reducing radiated emissions. For example, reducing a trace from 5 cm to 1 cm for a 10 GHz signal (wavelength ~1.4 cm in FR4) can decrease the radiated field strength by up to five times, thanks to its linear dependence on length, while significantly reducing radiated power. This simple layout change, effectively reduces emissions by minimizing loop areas, and avoiding resonance, especially when traces are kept away from board edges.
Simulate Before Building:
Pre-layout simulation has emerged as a critical step in the PCB design process, enabling proactive EMI management. Employ advanced electromagnetic tools like SIMBEOR® to model EM field distributions and pinpoint potential emission hotspots, such as those arising from impedance mismatches or poor field containment. A brief simulation can expose risks, for example, a trace near the board edge radiating energy or a stackup lacking sufficient return and reference planes compromising return paths, before they escalate into costly EMI or compliance failures. Dedicating time to this analysis proves far more economical than post-fabrication redesigns, preserving both project timelines and resources by addressing issues at the earliest stage.
Gain Mastery Over Your PCB's EMI Future
EMI doesn't need to impact your designs. By focusing on optimizing stackup, preserving impedance continuity, ensuring signal reference integrity, and designing layouts with EM field awareness, you can avoid PCB EMI problems. With modern "grounding" techniques and simulation software, designing low-EMI boards from the beginning is easier than ever, thanks to the available tools and expertise.
Want to learn more? Our Online Training Courses & EMI Control Guides offer detailed techniques and workflows to tackle EMI at its source. They are filled with step-by-step solutions specifically designed for engineers who encounter these challenges regularly. Check out our course and guides here and move towards EMI-free designs.