Signal Integrity: The Key to EMC Compliance for Electronic Engineers
- Dario Fresu
- 3 days ago
- 8 min read
Consider this scenario: You're an electronic engineer nearing the completion of a product design. After months of meticulous effort—covering schematic capture, PCB layout, and prototype validation—you expect to pass the EMC test with flying colors. Instead, the report is a shock: excessive radiated emissions, breaching standards like FCC Part 15 or CISPR 32. Now, you're dealing with a redesign, a delayed launch, and costs surpassing $10,000 for new boards and retesting. What went wrong? Frequently, the root of the problem lies in signal integrity—a vital yet often neglected facet of electromagnetic compatibility (EMC).
Why Signal Integrity Matters for EMC
EMC compliance is essential both legally and practically: devices must operate together without emitting noise beyond regulatory limits or failing susceptibility tests. To ensure compliance, a PCB must facilitate smooth signal propagation, preventing energy leakage as EMI and resisting external interference. Maintaining signal integrity is crucial for managing electromagnetic field behavior within the board. Neglecting signal integrity can result in increased radiated and conducted emissions, threatening compliance and escalating project costs.
Three key factors influence this process: return and reference plane integrity, crosstalk, and trace impedance. These are not just theoretical concepts—they are design choices you can optimize. By mastering them, you can avoid the expensive cycle of EMC failures, delivering boards that perform reliably and meet standards like EN 55032. Let’s examine each in detail.
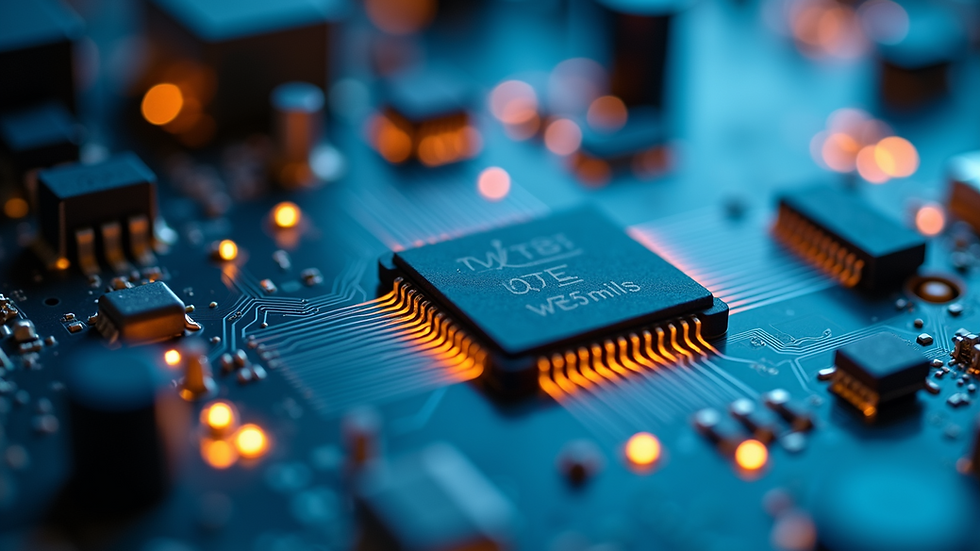
Reference Plane Integrity
Reference plane integrity entails maintaining a continuous, low-impedance reference plane—typically called "ground"—beneath every signal trace. Signals propagate as electromagnetic fields that couple to this plane, establishing a controlled return path. Disruptions such as plane splits or missing vias break this containment, increasing radiated emissions.
A solid return and reference plane (RRP) ensures return currents align closely with the signal trace, minimizing loop area and magnetic field strength. Without this continuity, currents detour—for example, around a split plane—enlarging the loop and radiating energy. At 1 GHz (wavelength ~14 cm in FR4), a 5 cm detour versus a 0.5 cm loop could increase emissions by up to 20 dBµV/m, exceeding limits like CISPR 32 (~40 dBµV/m).
Steps to Address It
Stitching Vias: Place a RRP-connected via within lambda/20 (e.g., 0.7 mm at 10 GHz in FR4, where lambda is approximately 1.4 cm) of each signal via during layer transitions. This minimizes the return path length, reducing via inductance from approximately 10 nH for a 1 cm detour to less than 1 nH, curbing EMI.
Continuous Planes: Route high-speed signals over unbroken return and reference planes. A split beneath a trace can double the loop area, increasing radiated emissions.
Transition Checks: Verify that layer switches for high-speed signals maintain reference continuity—omitting a via transforms the trace into an unintentional radiator.
By ensuring reference plane integrity, you confine magnetic fields and reduce radiated emissions, enhancing EMC compliance.
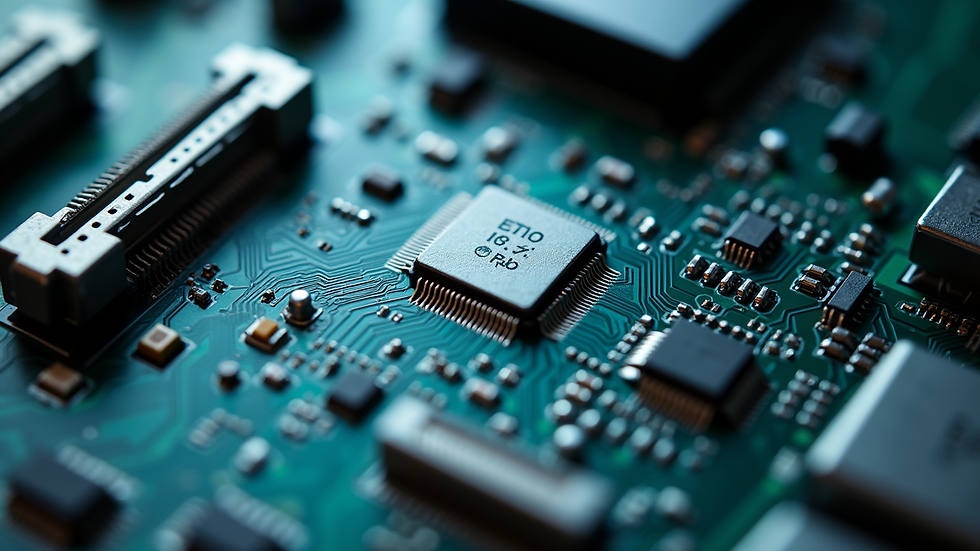
3. Crosstalk
Crosstalk is the unintentional coupling of electromagnetic fields between adjacent traces. An aggressor trace’s electric field (via capacitance) or magnetic field (via inductance) induces noise in a victim trace, degrading signal quality. Beyond signal corruption, crosstalk contributes to EMI: noise coupled to I/O cables acts as an antenna, radiating emissions.
At 500 MHz, 10 mV of crosstalk on a 5 cm cable could elevate radiated noise by approximately 10 dBµV/m, potentially exceeding CISPR 32 Class B limits (~40 dBµV/m). The compact trace layout, with minimal spacing, increases crosstalk and leads to violations in radiated emissions.
Steps to Address It
Increase Spacing: Space adjacent traces at least three times their width (e.g., 0.3 mm for a 0.1 mm trace) to weaken electric field coupling, reducing mutual capacitance by 50–60%. This minimizes crosstalk by limiting the charge induced between traces.
Reference Planes: Place a solid RRP directly beneath traces, with minimal dielectric spacing (e.g., 0.2 mm), to shield electric fields and confine magnetic fields, reducing crosstalk coupling by 10–20 dB. This enhances isolation between signal layers and paths.
Differential Pairs: Implement differential signaling for high-speed interfaces (e.g., USB’s 90-ohm pairs) to reject common-mode noise through signal subtraction, significantly lowering crosstalk susceptibility in noisy environments.
Filtering: Install ferrite beads or low-pass filters on I/O lines to attenuate coupled high-frequency noise, preventing its radiation via cables or entry into the board from external sources.
By mitigating crosstalk, these steps preserve signal integrity and ensure emissions remain within EMC-compliant limits.
4. Trace Impedance
Trace impedance refers to the characteristic impedance (Z0) of a signal path, which is influenced by factors such as trace width, thickness, and the dielectric properties of the stackup, including permittivity (e.g., FR4’s ϵr is approximately 4.5) and layer spacing. Typical targets are 50 ohms for single-ended signals and 100 ohms for differential pairs. Impedance mismatches can cause energy reflection, leading to ringing and EMI.
For instance, when a 50-ohm trace encounters a 60-ohm via, the reflection coefficient Γ (Gamma) = (Z2+Z1)/(Z2−Z1) = (60 - 50) / (60 + 50) = 0.09, meaning 9% of the voltage is reflected. At 3 GHz (with a wavelength of about 4.7 cm in FR4), this can lead to radiation if it couples with a resonant trace (e.g., 2.4 cm, approximately λ/2), potentially increasing emissions by 5–10 dBµV/m and surpassing CISPR 32 limits. Variations in trace widths can exacerbate these reflections, contributing to failures in radiated emissions.
Steps to Address It
Calculate Trace Width: Use a simple online tool like a microstrip calculator to figure out the right trace width for your desired impedance, such as 50 ohms for single-ended signals. For example, on a 0.2 mm thick FR4 board, a 0.18 mm wide trace over a return and reference plane gets you close to 50 ohms. The fundamental here is matching the trace to the system so signals travel smoothly without bouncing back.
Maintain Consistency: Keep the trace width, board thickness, and RRP steady along the signal path. Changes—like narrowing the trace or hitting a gap in the plane—mess up the impedance, causing part of the signal to reflect. For vias, back-drilling removes extra stubs that act like dead-end pipes, adding unwanted impedance and noise. Consistency keeps the signal flowing clean and quiet.
Simulate Impedance: Use a tool such as SIMBEOR® to verify your impedance prior to constructing the board. These programs analyze your traces, vias, and layers to identify issues that could reflect, for instance, 9% of the signal and introduce 5–10 dBµV/m of radiated noise at 1 GHz if it encounters something that amplifies it, like a long trace. The goal is to detect problems early to avoid uncertainty about what went wrong after the board is built.
By keeping trace impedance stable, you stop reflections that distort signals and create EMI, ensuring clear transmission and an EMC-friendly design without expensive do-overs.

5. Using Software Tools for Analysis
Performing manual signal integrity checks on complex circuit boards is highly challenging. The intricacy of contemporary electronic designs introduces numerous variables that can impact performance, making it increasingly hard to detect issues without advanced tools. Manual inspections are not only time-consuming but also susceptible to human error, potentially leading to overlooked problems that could compromise the entire system's integrity.
Tools like SIMBEOR® have revolutionized this process by quickly simulating electromagnetic fields, impedance, and crosstalk. During our live demo sessions, we detected thousands of errors within minutes on a board that had missing vias, crosstalk hotspots, and impedance mismatches.
Benefits
The advantages of utilizing advanced simulation tools in electromagnetic compatibility (EMC) design are numerous and impactful. Below are some key benefits that highlight their significance in the design process.
Spot Issues: Detailed reports generated by these tools are instrumental in identifying potential violations. By pinpointing such problems early in the design phase, engineers can make informed decisions to rectify them before they escalate into costly redesigns.
Guide Fixes: These tools provide actionable insights by suggesting specific adjustments in placement or spacing. With precision guidance, designers can optimize component layouts to minimize electromagnetic interference (EMI). This targeted approach not only enhances performance but also streamlines the design process, ensuring compliance with regulatory standards.
Visualize Fields: Electromagnetic field plots generated by simulation software are invaluable for visualizing potential leakage risks. For instance, a split plane may exhibit a radiation spike in certain areas, indicating where interference could occur. By visualizing these fields, engineers can take proactive measures to mitigate risks, ensuring the integrity of the device's operation in real-world environments.
These tools amplify your expertise rather than replace it. A deep understanding of why specific design choices, such as stitching vias, are essential allows you to act decisively on simulation data. This comprehension accelerates the development of EMC-ready designs, ultimately leading to more reliable and efficient electronic products.
6. Importance of Proper Stack-Up Design
The arrangement and materials of the PCB stackup influence signal integrity and electromagnetic interference (EMI). A poorly designed stackup can lead to increased emissions, while a well-designed one helps to contain them.
Two-Layer vs. Four-Layer Boards
Two-layer boards without dedicated planes compel signals to reference other traces, creating large loops. A four-layer stackup with dedicated return and reference planes confines the fields, significantly reducing emissions and directing the energy carried by the EM fields to their intended destinations.
Best Practices
Adjacent Planes: Pair each signal layer with a nearby return and reference plane to tightly control electromagnetic fields. The goal is to sandwich the signal between planes, keeping electric and magnetic fields locked in rather than letting them spread out and radiate. This containment keeps emissions low and signals stable.
No Splits: Never route signals over gaps or splits in reference planes, as these interruptions force return currents off course, weakening signal integrity along the entire path. When a high-speed signal hits a split, the current has to detour around it, creating a larger loop that pumps out more noise. Avoiding these gaps keeps the signal steady and prevents extra radiation that could fail EMC tests.
Via Stitching: Add return and reference vias (RRV) near each signal via to link reference planes across layers. This gives the return current a quick, direct route back to its plane, especially when jumping between layers. Without a stitching via, the current might take a long, winding path, stirring up unwanted noise. Placing vias close to signal transitions keeps fields in check and cuts down on EMI with a simple, low-cost fix.
Dielectrics: Pick dielectric materials and thicknesses that keep impedance steady and signal loss low. FR4 is a go-to choice, but its thickness between signal and ground layers needs to match your trace design—like a thinner layer for tighter impedance control. A mismatched dielectric can throw off the signal’s behavior or let energy leak away, while a well-balanced one ensures the trace performs reliably and keeps EMI in line across different frequencies.
Four-layer boards cost more upfront—think a few dollars extra per board compared to two-layer ones—but they’re a compliance steal over time. Two-layer designs, often stumble in EMC tests, leading to thousands in rework, EMI troubleshooting, and repeat testing fees. Four-layer boards, with dedicated RRP, knock down emissions from the start, saving weeks of headaches and big money on fixes. The extra cost upfront pays off by getting compliance right the first time.
Focus on Fundamentals
Electromagnetic Compatibility (EMC) compliance fundamentally relies on the principles of signal integrity. By implementing particular design strategies, engineers can efficiently control electromagnetic interference and improve the reliability of their electronic products. As we have observed, essential strategies include:
Reference Plane Integrity: Utilizing continuous reference planes and strategically placed vias helps contain electromagnetic fields, reducing noise and improving signal quality.
Crosstalk Reduction: Properly spacing traces and their RRPs minimizes unwanted coupling between signal lines, which is crucial for maintaining signal integrity.
Trace Impedance Control: Ensuring that the characteristic impedance (Z0) of traces is matched prevents signal reflections that can lead to data corruption and performance issues.
Solid Stackup: Creating a robust stackup provides a reliable foundation for the entire circuit board, supporting both performance and compliance.
By implementing these strategies and using advanced tools like SIMBEOR®, designers can transform EMC compliance from a challenging task into an integral part of the design process. When starting your next project, applying these principles will lead to circuit boards that not only function effectively but also meet compliance standards from the outset. If you're keen on mastering EMI control techniques to expedite EMC compliance, we encourage you to explore our online training courses and EMI control guides.