Mastering PCB Design with IPC-2221: The Industry’s Foundational Standard
- Dario Fresu
- Apr 8
- 4 min read
The field of printed circuit board (PCB) design requires a careful balance between electrical performance, mechanical integrity, and manufacturability. For more than two decades, a key standard has played a crucial role in this area: IPC-2221, known as the "Generic Standard on Printed Board Design." Initially published in 1998 by IPC (Association Connecting Electronics Industries), it has undergone updates with revisions such as IPC-2221B in 2012, and the latest IPC-2221C, acting not only as a guideline but as a comprehensive framework that links theoretical design with practical production.
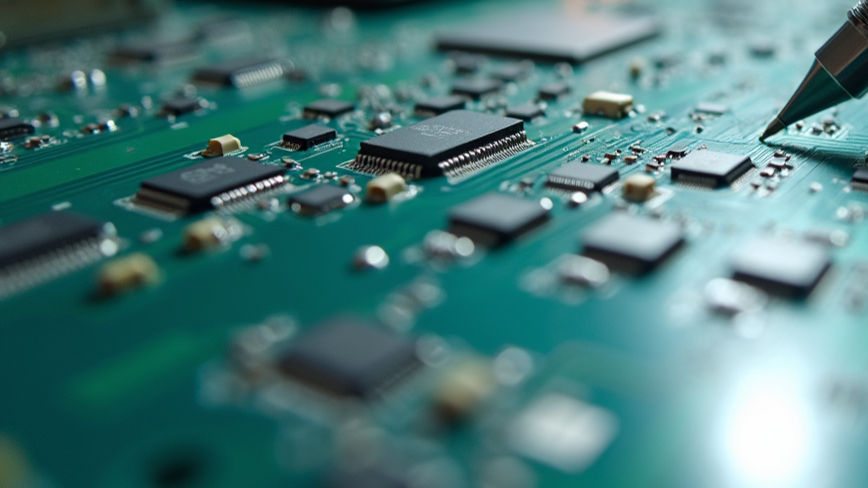
As the foundational element of the IPC-2220 series, which includes standards such as IPC-2222 for rigid PCBs and IPC-2223 for flexible designs, IPC-2221 provides universal principles relevant to all board types. Whether you are an experienced designer or a technician new to the field, understanding this standard is crucial for meeting the requirements of contemporary electronics. Let's explore its scope, technical insights, and practical significance.
The Scope and Structure of IPC-2221
IIPC-2221 applies to a wide range of PCBs, rigid, flexible, and high-density interconnect (HDI), covering single-sided, double-sided, and multilayer designs made from organic materials. Its versatility makes it the go-to reference for projects of any scale or complexity.
In its latest Revision C, as of April 2025, the standard covers over 180 pages, addressing every design aspect such as material selection, electrical clearances, thermal management, and mechanical integrity. Although it's challenging to read, this complexity is advantageous. The detailed technical content provides a structured approach to PCB design, ensuring engineers consider both broad principles and the intricate details that can determine a board's success or failure.
The Importance of Design Guidelines
The design guidelines specified in IPC-2221 are created based on extensive industry research, expert contributions, and practical insights gained from years of field experience. These guidelines help engineers prevent common errors that could lead to costly production mistakes or subpar performance.
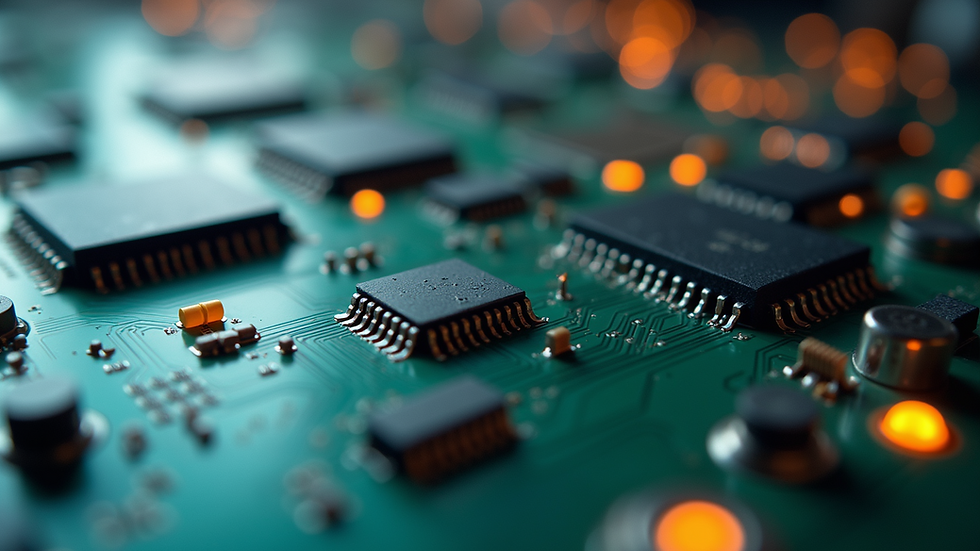
For instance, a key subject covered by IPC-2221 is the concept of trace width calculation. It emphasizes that PCB traces must be sufficiently wide to handle current without leading to overheating. A simple formula is provided to calculate the required width, taking into account factors like current load and allowable temperature rise. Following these guidelines helps designers prevent thermal issues that could compromise the PCB's functionality.
Choosing Materials: The Foundation of PCB Design
Choosing the right materials is crucial for the success of a PCB project, and IPC-2221 provides engineers with the essential criteria for making informed choices. The standard describes different material types, such as epoxy resin and polyimide, highlighting their benefits and drawbacks.
Engineers must also take into account the dielectric constant and its effect on signal integrity. For high-speed applications, materials with lower dielectric constants are typically recommended to reduce signal loss. IPC-2221 offers guidance to help engineers select materials that meet their project needs while ensuring reliability and performance.
Additionally, the document stresses the significance of environmental conditions. Factors like humidity and temperature can influence the properties of the materials used. Understanding these factors enables engineers to choose materials that will perform effectively in their intended environments, thereby improving product longevity and performance.
Effective Thermal Management Strategies
Effective thermal management is essential for the durability and reliability of PCBs. IPC-2221 offers valuable insights and guidelines for efficient thermal design by suggesting heat dissipation methods. These techniques are increasingly important as components become more compact and powerful.
Appropriate thermal management strategies can involve using heat sinks, ensuring sufficient spacing between heat-generating components, and incorporating thermal vias. This guideline helps ensure efficient heat dissipation, decreasing the risk of component failure and improving overall performance.
Furthermore, the standard emphasizes the importance of thermal simulations. These simulations can forecast how a PCB will respond to thermal stress, enabling more informed decision-making during the design phase. By employing these techniques, engineers can proactively tackle thermal challenges rather than addressing them after production.
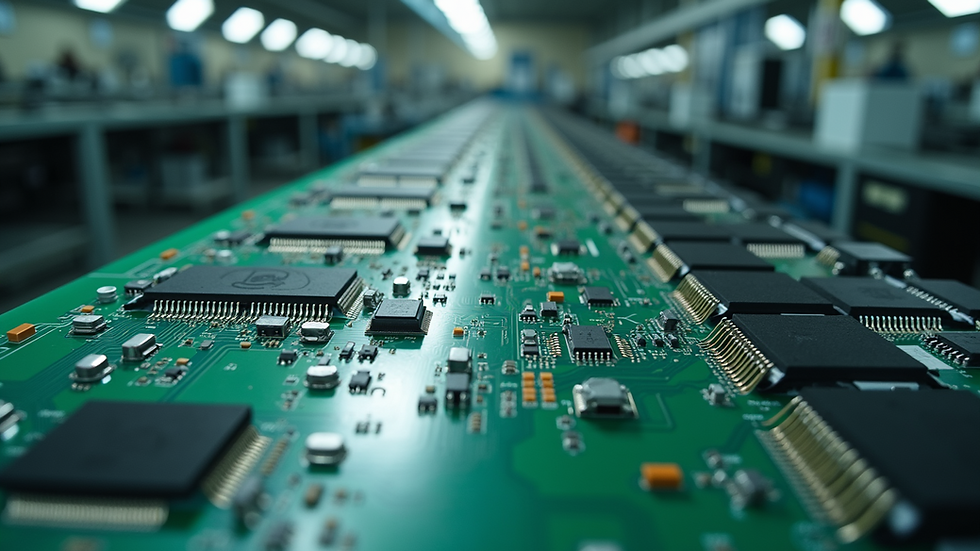
Quality Assurance and Testing Protocols
By following IPC-2221, designers not only create durable PCBs but also enhance quality assurance and testing protocols. This standard includes testing methods to ensure that the boards meet specified parameters and can perform effectively under the intended operating conditions.
The testing protocols outlined in IPC-2221 include procedures for electrical performance tests, thermal cycling, and mechanical integrity assessments. These methods are crucial for confirming that a PCB complies with its design specifications and can operate reliably throughout its expected lifecycle.
Additionally, understanding these testing protocols encourages engineers to adopt design for test (DFT) best practices. By designing PCBs that are easy to test, companies can save time and reduce costs related to late-stage design changes or recalls.
Final Thoughts: The Path Forward in PCB Design
Becoming proficient in PCB design with IPC-2221 involves more than just understanding its guidelines; it requires applying this knowledge to develop efficient, reliable, and high-performance printed circuit boards. As technology advances and demands on PCBs increase, the importance of IPC-2221 remains strong. By embracing the principles in IPC-2221, engineers can improve their design processes, fostering the creation of innovative products capable of enduring the challenges of modern technology.
Achieving expertise in PCB design involves a dedication to quality, adherence to standards, and a commitment to continuous learning. At Fresu Electronics, we are dedicated to helping engineers grasp and implement best design practices from the outset. If you're interested in enhancing your skills, feel free to explore our courses and EMI control guides.
Comments